航空航天行業在1980年代開始使用3D打印技術。隨著近年來金屬3D打印技術的發展,它逐漸在 整個航空航天產業鏈中占據重要的戰略地位。由于金屬3D打印 制造對航空航天產業而言,具備 節省研發時間,輕量化設計,低成本制造集成化設計等先天優勢,因此應用這一技術,能夠使飛行器在未來能夠以更低的制造成本而獲得更好的性能。
應用實例
渦輪罩
傳統制造方式面臨的挑戰
在傳統制造采用各零部件分別鍛鑄,焊接成型后再精密加工的制造方式。自重大,制造和使用成本較高。
數字化金屬3D打印制造
采用數字化設計并進行結構優化,將需要分別制造的零部件集成于一體,應用基于MPBF TM技術的M650四激光金屬增材制造系統熔化金屬粉末,以不亞于鍛鑄成型的金屬致密度直接打印制造功能集成化、高精度的渦輪部件。制造完成的部件具備傳統制造方式不可能完成的復雜三維點陣鏤空結構,不僅大幅降低了部件自重,還有利于在高溫高 壓的使用環境中快速散熱。在保證部件強度的同時,還提高了部件的性能。
成品:
渦輪罩
航空機匣
傳統制造方式
在采用鍛鑄等傳統制造方式制造航空器常用的大尺寸、薄壁結構部件時,很難一次性或批量制造出性能完善的產品。
數字化解決方案:
采用數字化設計,將多種功能組件集成為一體,并應用基于MPBFTM技術的M450 金屬增材制造系統融化金屬粉末,以不亞于鑄造的金屬致密度直接快速制造功能一體集成、重量大幅降低、高精度的機匣。
成品:

航空燃油噴嘴
傳統制造存在的問題
飛機發動機燃油噴嘴,體積小,但結構復雜,內含復雜流道,傳統制造方式都是拆解成多造 個零部件分別制造后組裝,周期長,制造成本高。
數字化解決方案
采用耐高溫的鎳基合金IN718進行數字化直接制造如下圖所示的噴嘴,金屬3D打印批量制造每36小時可以批量生產一個批次的產品,且不需后期組裝工序,生產效率大幅增長
制造成果
金屬3D打印制造產品重量減輕了25% ,內部具備最優化的燃油流道,顯著提高工效并降低油耗。金屬3D打印制造產品的零部件一體化程度高,零件從原先的18個下降到了現在的僅僅1個,不再需要后期組裝。金屬3D打印制造產品具有復雜但合理的內部冷卻通道,耐久性較原來提高了5倍,工作壽命更長。
成品:
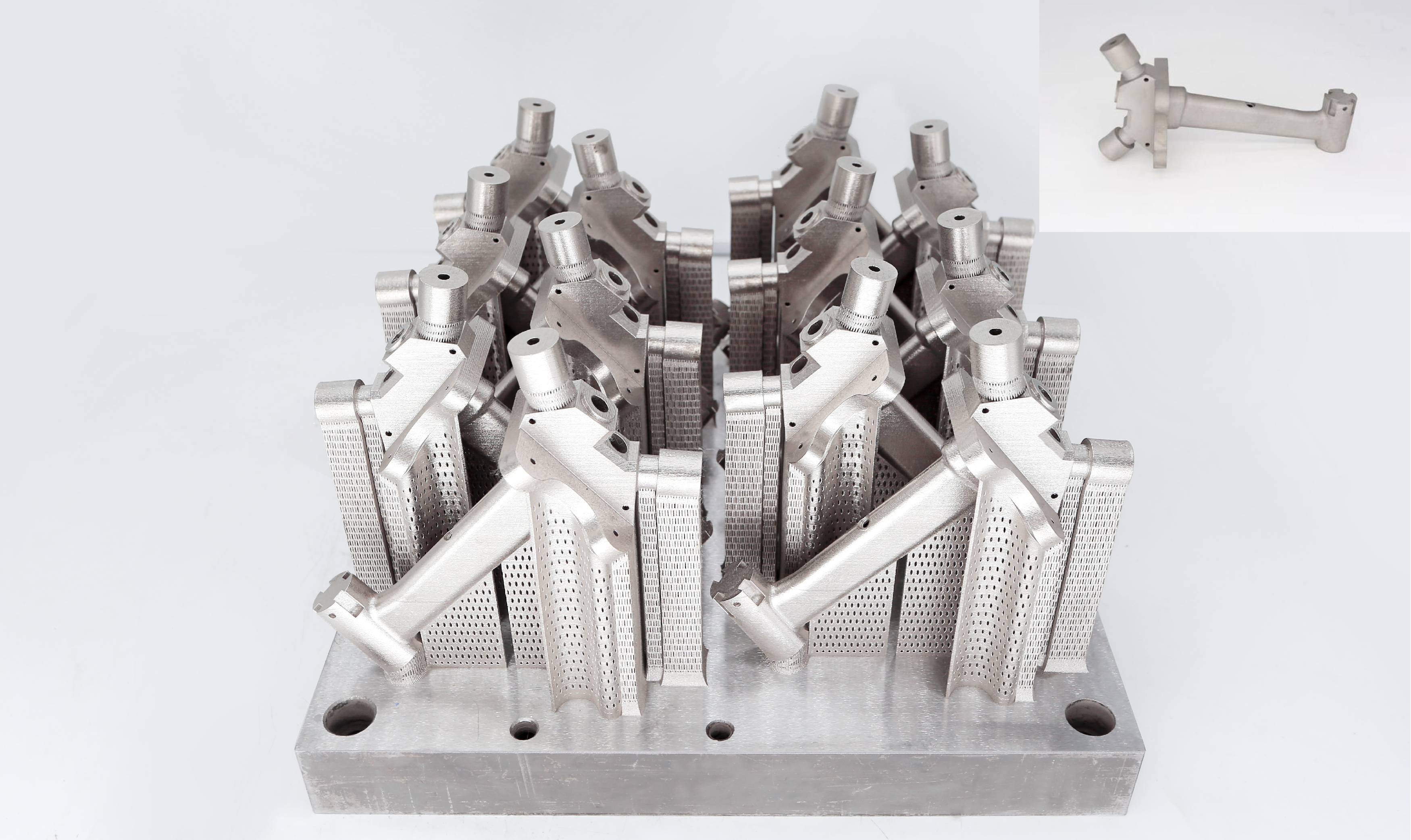
航空燃油噴嘴
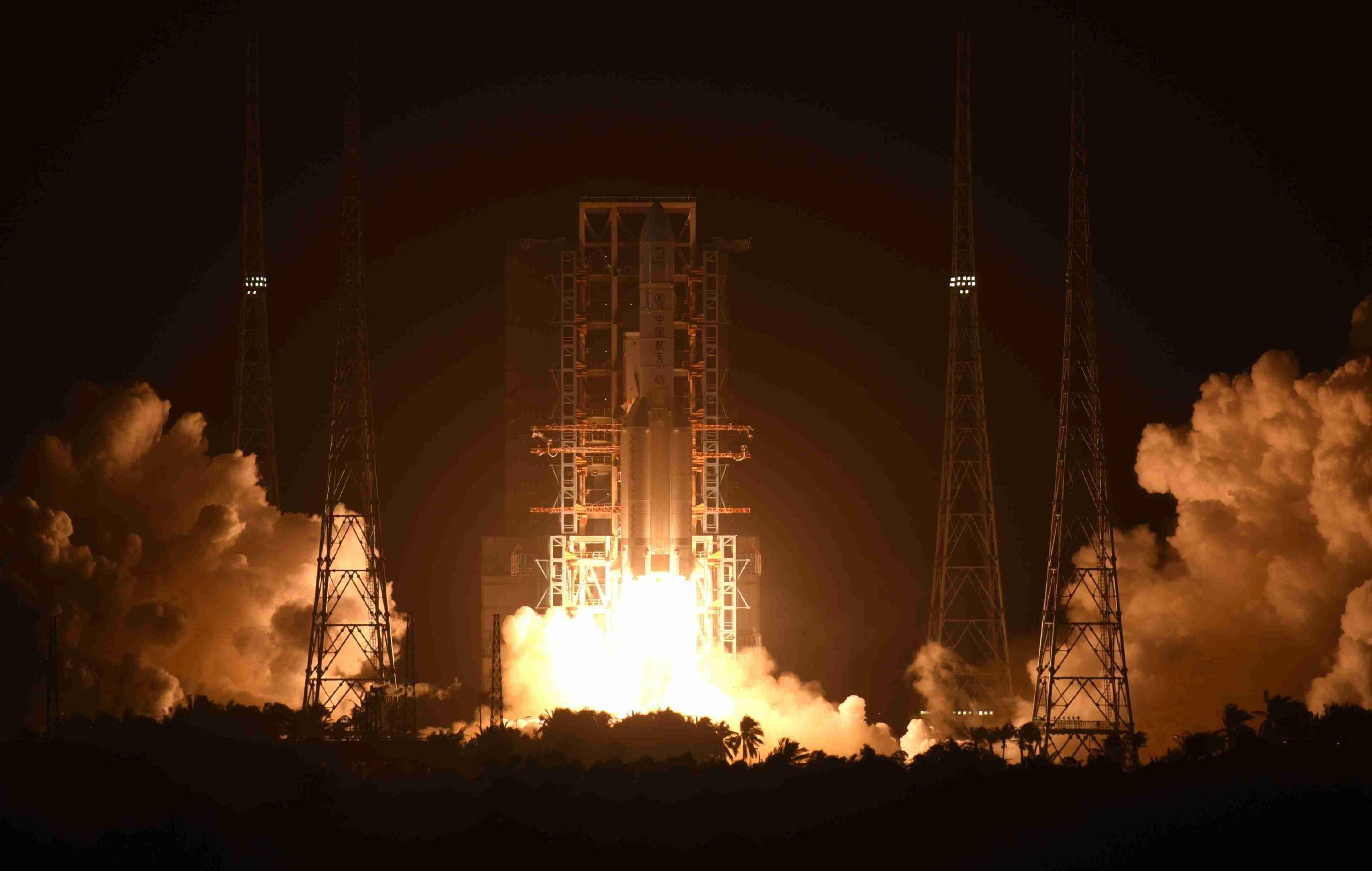
縮短研發周期
金屬3D打印制造技術讓高性能金屬零部件,尤其是高性能大結構件的制造流程大為縮短。無需為零部件在制造過程中開發新工藝、新模具,這將極大的縮短產品的研發制造周期。
提高材料利用率
金屬3D打印制造技術可以直接制造出任意形狀的零部件,且成品只需進行少量的后續處理即可投入使用,材料的使用率達到了60%—90%。
優化結構、降低重量、增加壽命
金屬3D打印制造技術可以優化部件的結構從而減輕重量。且通過結構優化,能使部件的應力呈現出最合理分布,從而增加使用壽命。
零部件修復成型
金屬3D打印制造技術可應用于金屬部件的修復中,其修復的過程事實上是增材制造過程的延續,部件修復區與部件受損區可以達到最優的匹配,且性能滿足甚至是高于基材使用性能。
在航空航天行業中應用金屬3D打印制造技術,可以直接制造尺寸巨大、結構復雜的高密度零部件,與傳統鑄造方式相比,制造時間被大大縮短。
隨著金屬3D打印制造技術的不斷發展,易加三維將繼續與國內外航空航天行業用戶保持合作并不斷創新。